Ultrasonic NDT in Aerospace
Non-destructive testing (NDT) is an indispensable component of the aviation industry, as it contributes to ensuring the safety of aircraft and other aerial vehicles. One of the most crucial techniques within NDT is ultrasonic testing, which enables precise inspection of components without causing damage. We collaborate closely with international experts in ultrasonic testing systems to ensure that your ultrasonic inspections are conducted at the highest level:
ScanMaster Systems IRT for inspection systems in immersion technology
ScanMaster specialises in submersible inspection systems, which are essential for the non-destructive testing of aerospace components. Their innovative technologies enable thorough underwater inspection to detect and evaluate even the smallest defects. ScanMaster’s immersion inspection systems are designed for high throughput and multi-shift operation in industrial and laboratory environments. Learn more
Air-coupled ultrasonic testing
Air-coupled UT enables precise inspection of highly attenuating materials that were previously difficult or impossible to access with conventional water-coupled ultrasonic testing methods. This allows for non-destructive and effective ultrasonic examination of modern composite materials such as GFRP and CFRP, as well as highly attenuating honeycomb structures used primarily in modern lightweight construction.
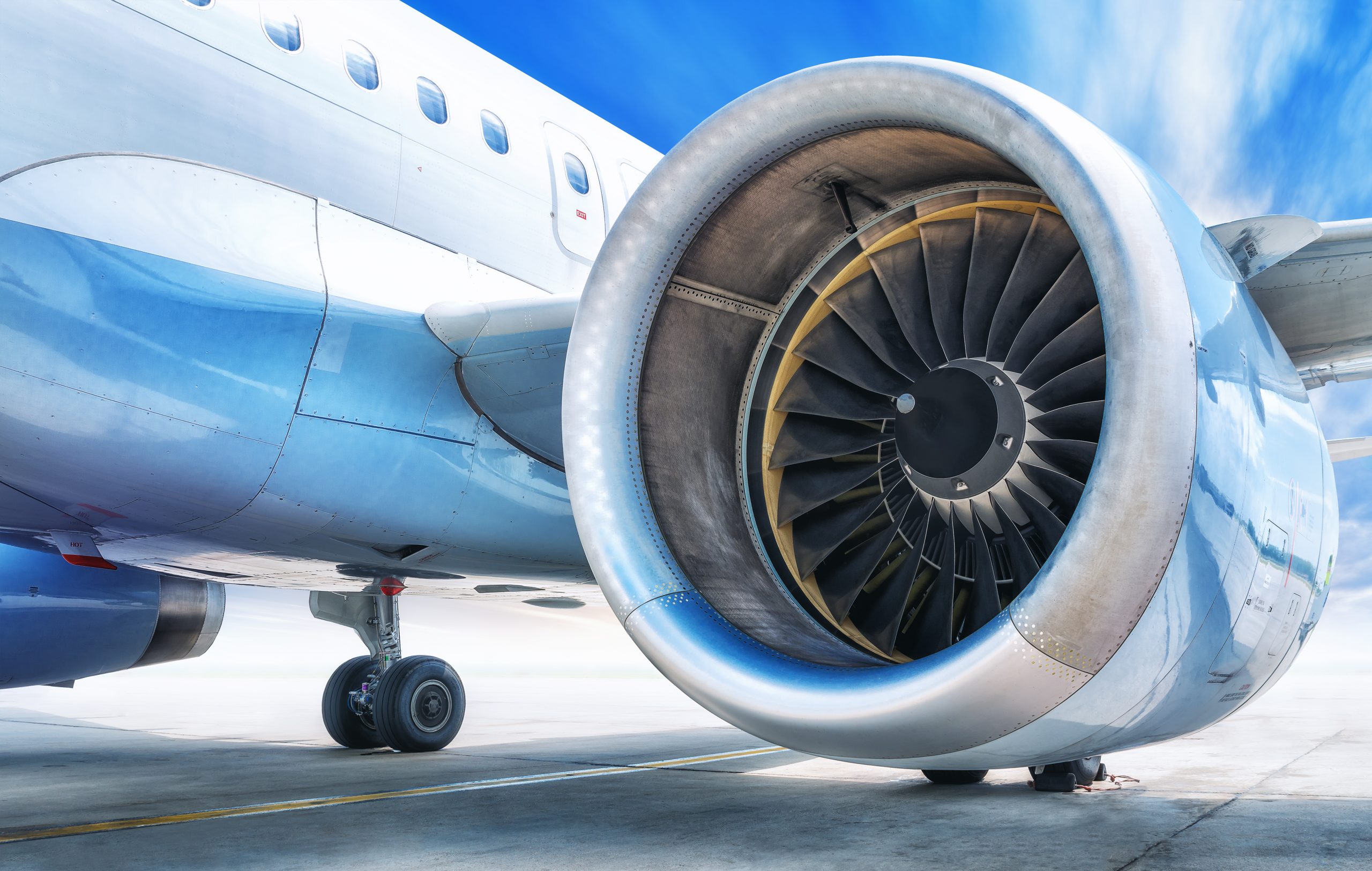
Advantages of Ultrasonic Testing in Aviation
By analysing the reflected ultrasonic waves, engineers can identify defects such as cracks, blowholes or porosity and determine their size, shape and position. Ultrasonic testing offers several advantages for the inspection of aerospace components:
- High accuracy and reliability: ultrasonic inspection enables precise localisation and characterisation of defects.
- Non-invasive inspection: Inspection can be performed without the need to destroy the sample.
- Early detection of damage: Regular ultrasonic inspections allow damage to be detected and repaired at an early stage before it leads to serious problems.
Your NDT Expert.
Metalworking | Railway | Aviation
FAQ's
-
What types of defects can be detected with ultrasonic testing?
-
How often should ultrasonic testing be carried out in aviation?
-
How can I ensure that my aircraft components comply with safety standards?
-
Why is non-destructive testing with ultrasound important in the aviation industry?
Any questions?
Actemium Cegelec Centre GmbH
Gutenstetter Street 14a
90449 Nuremberg
Phone: +49 (0) 911 9943-0
E-mail: info.nds@actemium.de